The chocolate bar packaging machine adopts the form of pillow packaging, which can automatically complete the whole process of feeding – bag making – sealing – printing batch number – finished product output – counting.
The chocolate bar wrapping machine adopts the original single-servo or double-servo motor control, which is more intelligent, has higher packaging precision, wider adjustable range, more precise control and better stability.
The Main Performance of Chocolate Bar Packaging Machine:
- Double frequency converter control. The bag length can be set and cut immediately, no need to adjust the idling, one step, saving time and film.
- Human-machine interface, parameter setting is convenient and quick.
- High-sensitivity photoelectric eye color mark tracking. And digital input of sealing and cutting position, so that the sealing and cutting position is more accurate.
- Independent temperature display control of each sealing area, suitable for a variety of different packaging materials.
- Positioning stop function, no sticking to the knife, no waste of film.
- The transmission system of the chocolate bar wrapping machine is simple, the work is more reliable, and the maintenance is more convenient.
- Fault self-diagnosis function, fault display is clear at a glance.
- All controls are realized by software, which is convenient for function adjustment and technical upgrade.
- All parts in contact with materials are made of stainless steel panels, which conform to food processing standards.
- The bag maker is adjustable, with long and short pitch settings, suitable for different sizes of packaging.
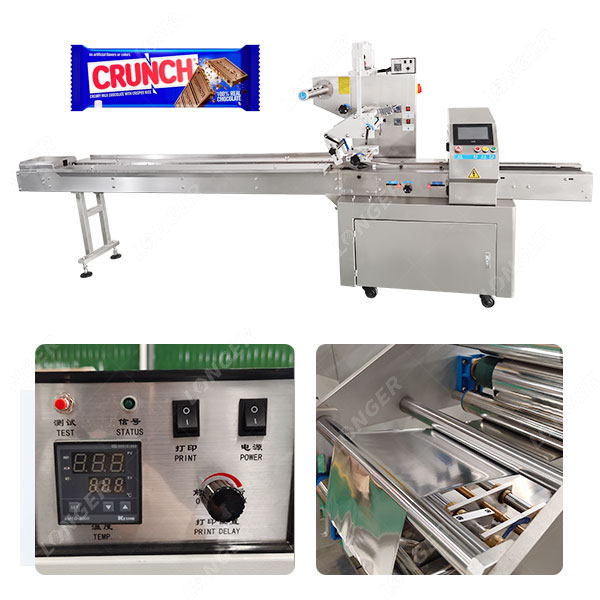
Scope of Application of Chocolate Bar Wrapping Machine:
It is suitable for the packaging of soft, long and loose objects. Such as towels, paper towels, vermicelli, egg rolls, sausages, squid, popsicles, fudge, biscuits, chocolate, etc.
Maintenance of Chocolate Bar Pillow Packaging Machine:
- After the new machine runs for one month, the operator should adjust the transmission chain and transmission belt every two months after operation;
- The main and driven gears of the horizontal seal should be filled with grease every two months or so;
- Clean the inside of the vertical sealing cover plate twice a week, and add lubricating oil to the vertical sealing sliding seat at the same time;
- The operator should regularly check whether the fastening parts are loose. Check and lubricate parts such as gears, racks, sprockets, chains and screw rods;
- Always clean and wipe the packaging machine cover, work surface and other outer surfaces to keep the machine clean.
Reviews
There are no reviews yet.